Details of Automotive Headlamp Mold Making
Automotive headlamp mold making is a complex and highly precise process, involving multiple technical stages. Below is a detailed breakdown of the steps and key aspects involved in the headlamp mold-making process.
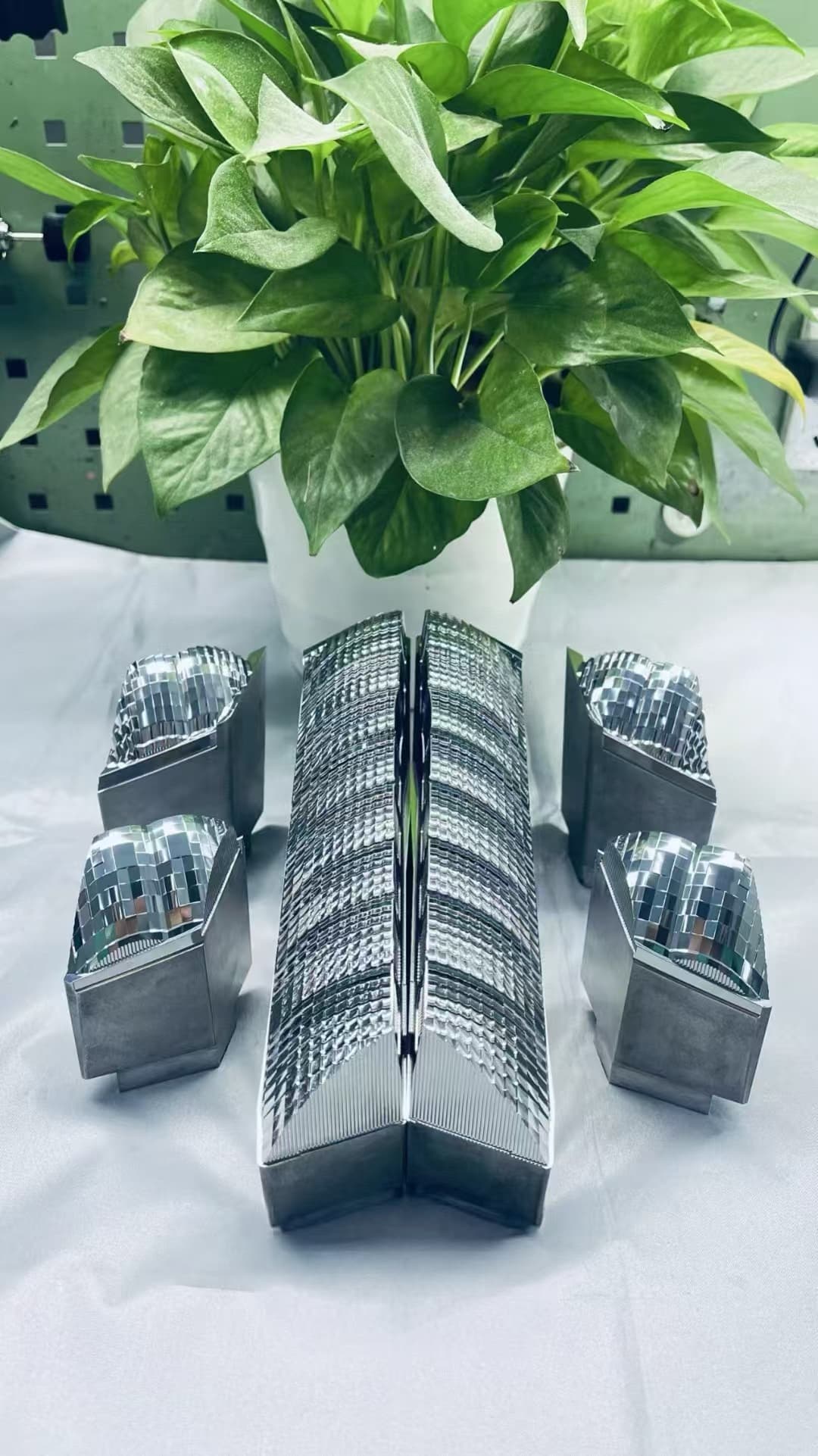
1. Design Phase
a. Exterior and Functional Design
- Exterior Design: The appearance of the headlamp must not only match the vehicle’s overall design style but also meet functional requirements. For example, front headlights need to provide adequate illumination, while tail lamps should ensure clear visibility.
- Optical Design: This includes the design of the light source, lenses, and reflectors. The optical design ensures that the light beam distribution, brightness, and scattering meet regulatory standards (such as uniform light distribution, optimal beam distance, etc.).
- Electrical Design: Modern headlamps often use LED, laser, or xenon light sources, and their electrical connections need to be safe and durable.
b. Mold Design
Mold design is critical to ensuring the headlamp’s shape, optical performance, and manufacturing efficiency. Key considerations include:
- Mold Structure: This includes the main mold body, cavities, cooling system, venting system, and gate design.
- Thermal Flow Analysis: Proper thermal management is crucial to ensure even material flow in the mold and prevent defects like air bubbles, cold spots, and uneven cooling.
- Assembly Considerations: Mold design must also consider ease of assembly, automation, and post-production testing or maintenance.
2. Material Selection
The choice of materials directly affects the optical performance, durability, and manufacturing process of the headlamp. Common materials used include:
- Transparent Materials (e.g., PC, PMMA): These materials are used for lenses or light covers because of their excellent transparency and impact resistance.
- Reflector Materials (e.g., Aluminum alloys, reflective films): Reflector parts require high reflectivity and are often made from aluminum alloys or specialized reflective coatings.
- Shell Materials (e.g., ABS, PC): The outer casing is usually made from ABS or PC due to their good impact resistance and processability.
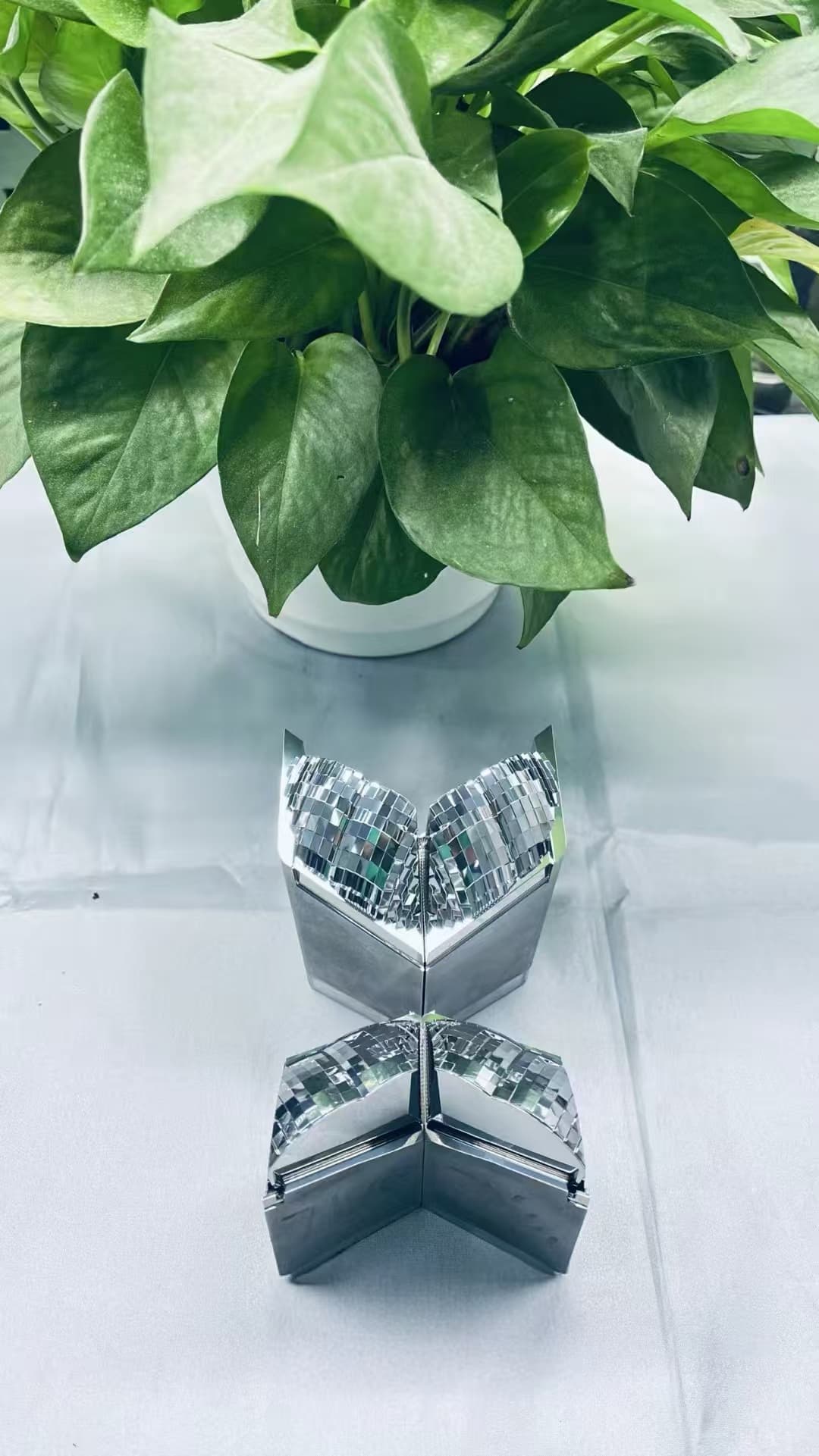
3. Mold Manufacturing
Manufacturing the mold for headlamp production requires high precision. Below are the types of molds commonly used and their manufacturing details:
a. Injection Molding
Injection molding is typically used for producing the outer shell and transparent parts (such as light covers or lenses). Key factors to consider:
- Gate Design: The gate position must avoid affecting the appearance of the headlamp and prevent defects like air pockets or cold shuts.
- Cooling System: Proper cooling design ensures uniform cooling of the plastic material, minimizing deformation.
- Mold Life: High-quality molds are usually made from high-hardness steel and undergo special heat treatment to increase their durability.
b. Die-Casting Molds
Die-casting molds are used for producing metal parts of the headlamp, such as aluminum reflectors. Considerations include:
- Metal Flowability: In the die-casting process, the molten metal needs to flow smoothly to prevent defects like voids or cracks.
- Cooling and Venting Systems: The die-casting mold needs to be designed with effective cooling channels to ensure uniform solidification of the metal. Venting is essential to prevent air pockets from forming inside the cast.
c. Optical Molds
Optical parts, like lenses, require molds with extremely high precision and surface quality. These molds usually require:
- Surface Polishing: Optical parts require a polished surface to ensure light clarity and transparency.
- Molding Process Control: The molding process, including temperature and pressure control, needs to be carefully monitored to avoid surface defects and optical performance issues.
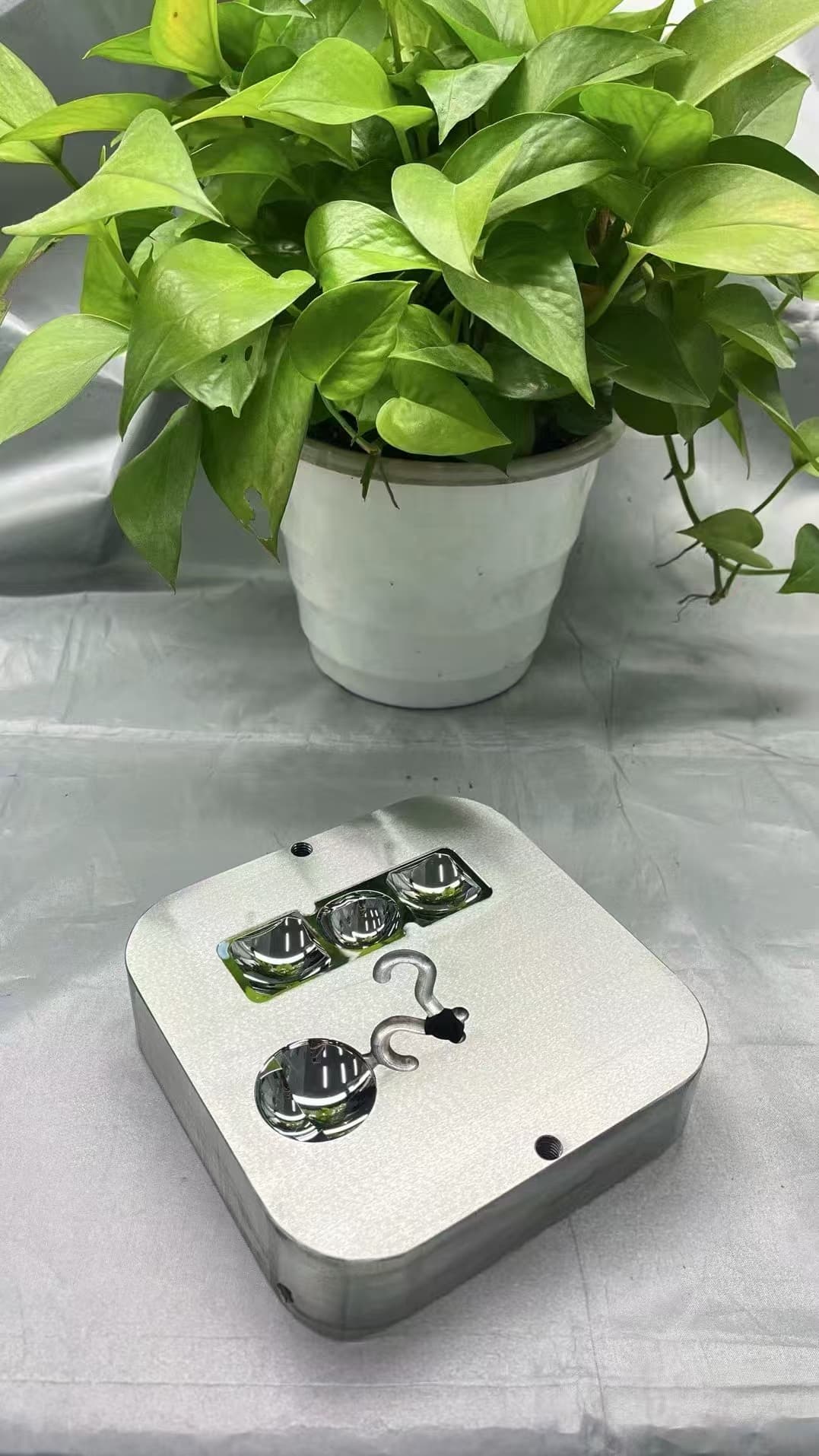
4. Mold Trial and Adjustment
Once the molds are fabricated, mold trials are conducted to test if the headlamp meets the design specifications. The objectives of the trial include:
- Checking Headlamp Appearance and Optical Performance: Ensuring that the shape, dimensions, and optical qualities match the design.
- Mold Adjustment: In the trial phase, adjustments to the gate, cooling system, and pressure are often required to eliminate potential defects such as air bubbles, surface marks, and deformations.
- Process Optimization: Ensuring that material flow is consistent and preventing issues like short shots, flash, or uneven cooling.
5. Production and Mass Manufacturing
Once the mold passes the trial phase, it proceeds to mass production. At this stage, attention must be paid to:
- Production Efficiency: The use of efficient automated equipment and high-precision molds ensures stable and consistent production of the headlamp.
- Quality Control: Every stage of production requires stringent quality control to ensure that each headlamp meets design standards, particularly regarding optical performance, appearance, and durability.
- Post-Processing: Some headlamps undergo additional processes such as polishing, painting, or printing of logos to ensure high aesthetic and functional quality.
6. Assembly and Testing
Once the headlamp parts are manufactured, assembly and testing are carried out:
- Optical Testing: This includes checking the light distribution, brightness, transparency, and overall optical performance to ensure they comply with safety standards.
- Mechanical Testing: The headlamp’s resistance to vibrations, shocks, and pressure is tested to ensure it can withstand real-world conditions in a moving vehicle.
- Electrical Testing: The electrical components, such as LED modules and connectors, are tested to ensure they function properly without faults.
7. Mold Maintenance and Optimization
Over time, molds experience wear and tear, leading to issues like deformation or reduced precision. Regular mold maintenance and optimization are crucial to:
- Maintain Production Stability: Ensuring that molds continue to produce parts with consistent quality and precision.
- Prolong Mold Life: Regular inspections, cleaning, and adjustments help extend the mold's lifespan and prevent breakdowns during production.
Summary
The automotive headlamp mold-making process involves various stages, including design, material selection, mold fabrication, trial production, mass manufacturing, assembly, and testing. Each stage requires precision and technical expertise to ensure that the final product meets the required performance, appearance, and safety standards. The entire process demands high-quality mold design and manufacturing, as well as comprehensive quality control.
If you have any further questions or require specific details about any part of the mold-making process, feel free to ask!