Mirror Optical Polishing: A Detailed Introduction
Jan 11, 2025
Mirror optical polishing is a processing technique that achieves a highly smooth, flawless surface to enhance the reflective and optical properties of an object. Below is a detailed explanation:
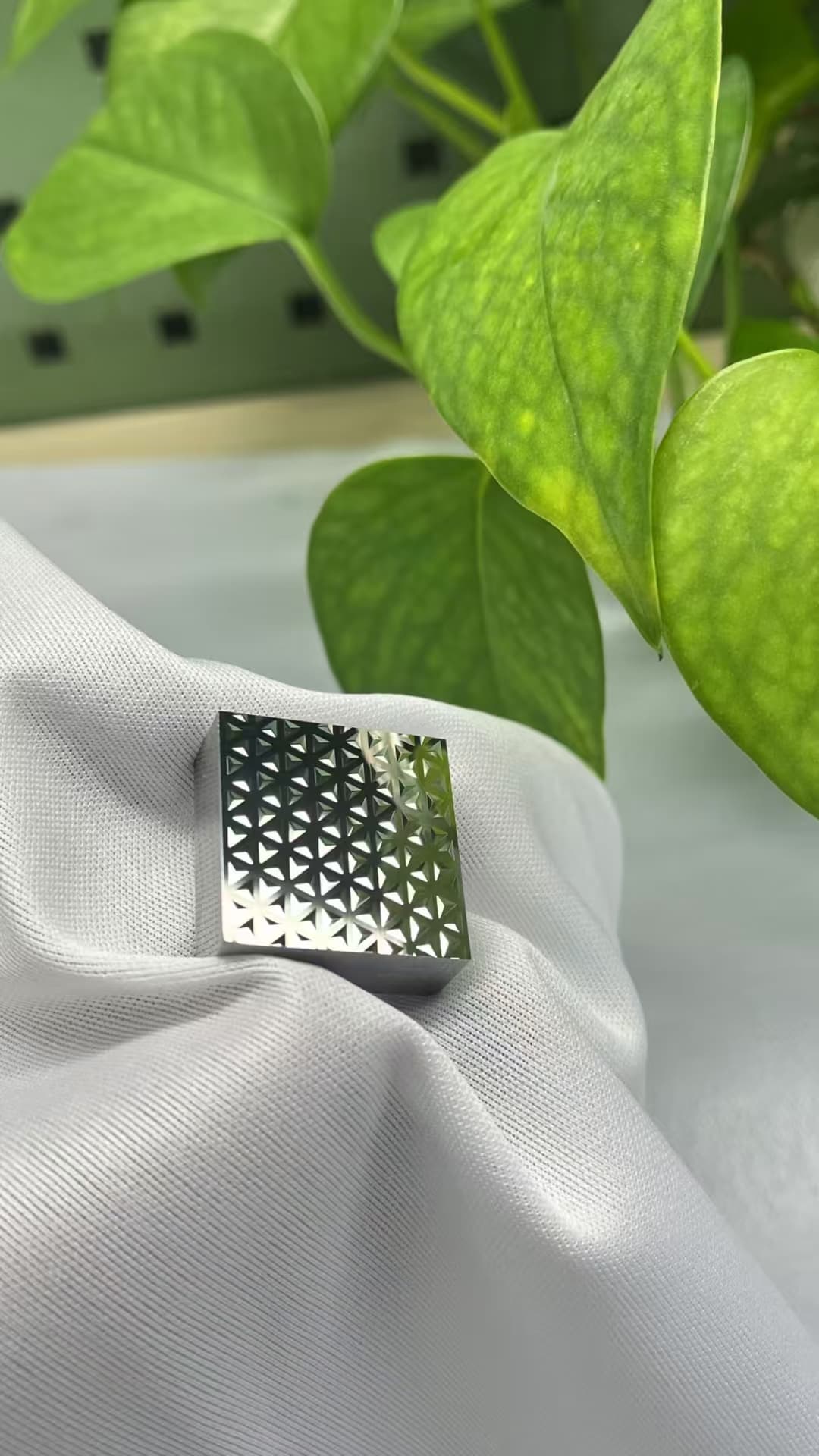
Primary Methods
- Mechanical Polishing: Achieved by cutting or plastic deformation of the material’s surface to remove protrusions and obtain a smooth surface. Common tools include oilstone sticks, wool wheels, and sandpaper. It is mostly manual, but specialized parts like rotating surfaces can use auxiliary tools such as turntables. For extremely high-quality requirements, ultra-precision polishing methods can achieve exceptional surface smoothness.
- Chemical Polishing: This method involves the preferential dissolution of microscopic protrusions in a chemical medium, resulting in a smooth surface. It does not require complex equipment and can polish complex-shaped workpieces efficiently. However, the surface roughness achieved is generally in the range of several tens of micrometers.
- Electrolytic Polishing: Similar in principle to chemical polishing, it involves selective dissolution of microscopic protrusions on the material surface, achieving a smoother finish. Compared to chemical polishing, it eliminates the effects of cathodic reactions, offering better results with a surface roughness of Ra < 1μm.
- Ultrasonic Polishing: The workpiece is placed in an abrasive suspension and exposed to ultrasonic vibrations, which cause the abrasives to polish the surface. It involves minimal macroscopic force, reducing deformation risks, but requires complex tooling and setup. This method can be combined with chemical or electrochemical techniques.
- Fluid Polishing: Utilizes high-speed liquid flow and its abrasive particles to polish the surface of the workpiece. Common techniques include abrasive jet machining, liquid jet machining, and fluid dynamic grinding.
- Controlled Flexible Polishing: Aimed at improving the controllability of optical processing, it uses flexible media like magnetorheological polishing fluids or ion beams as polishing tools. Corresponding equipment includes magnetorheological polishing machines and ion beam polishing machines.
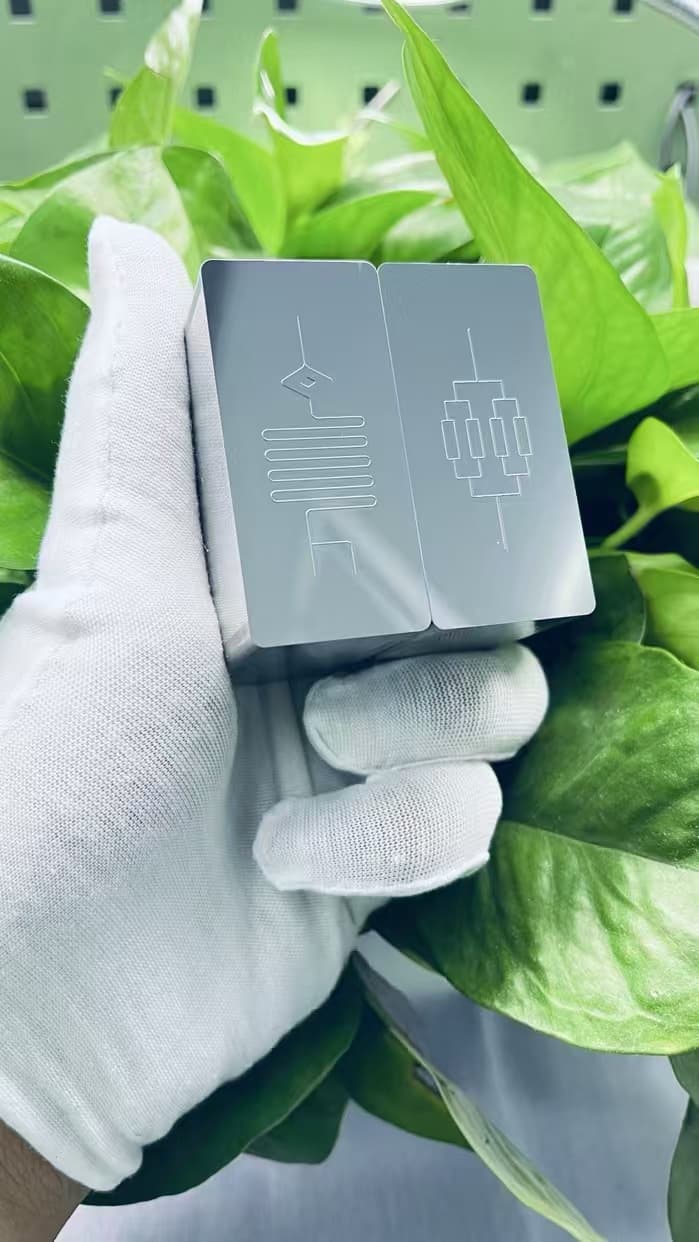
Basic Steps
- Cleaning: Completely remove dirt, impurities, grease, and oxidation layers from the object's surface using methods like chemical cleaning solutions or ultrasonic cleaning to prepare for polishing.
- Rough Grinding: Use coarse tools such as sandpaper, grinding cloth, or grinding discs to remove rough parts, scratches, and significant defects from the surface, achieving initial flatness.
- Intermediate Grinding: Based on the rough grinding step, use finer tools and materials, such as finer sandpaper or specific grinding liquids, to further refine the surface and reduce the traces left by rough grinding.
- Fine Grinding: Apply finer grinding tools, such as high-precision grinding discs or polishing powders, to achieve the desired smoothness and surface accuracy, laying the foundation for the final polishing step.
- Polishing: Use polishing tools like polishing wheels or polishing pads with polishing liquid, paste, or powder to finalize the treatment, enhancing surface gloss to achieve a mirror effect.
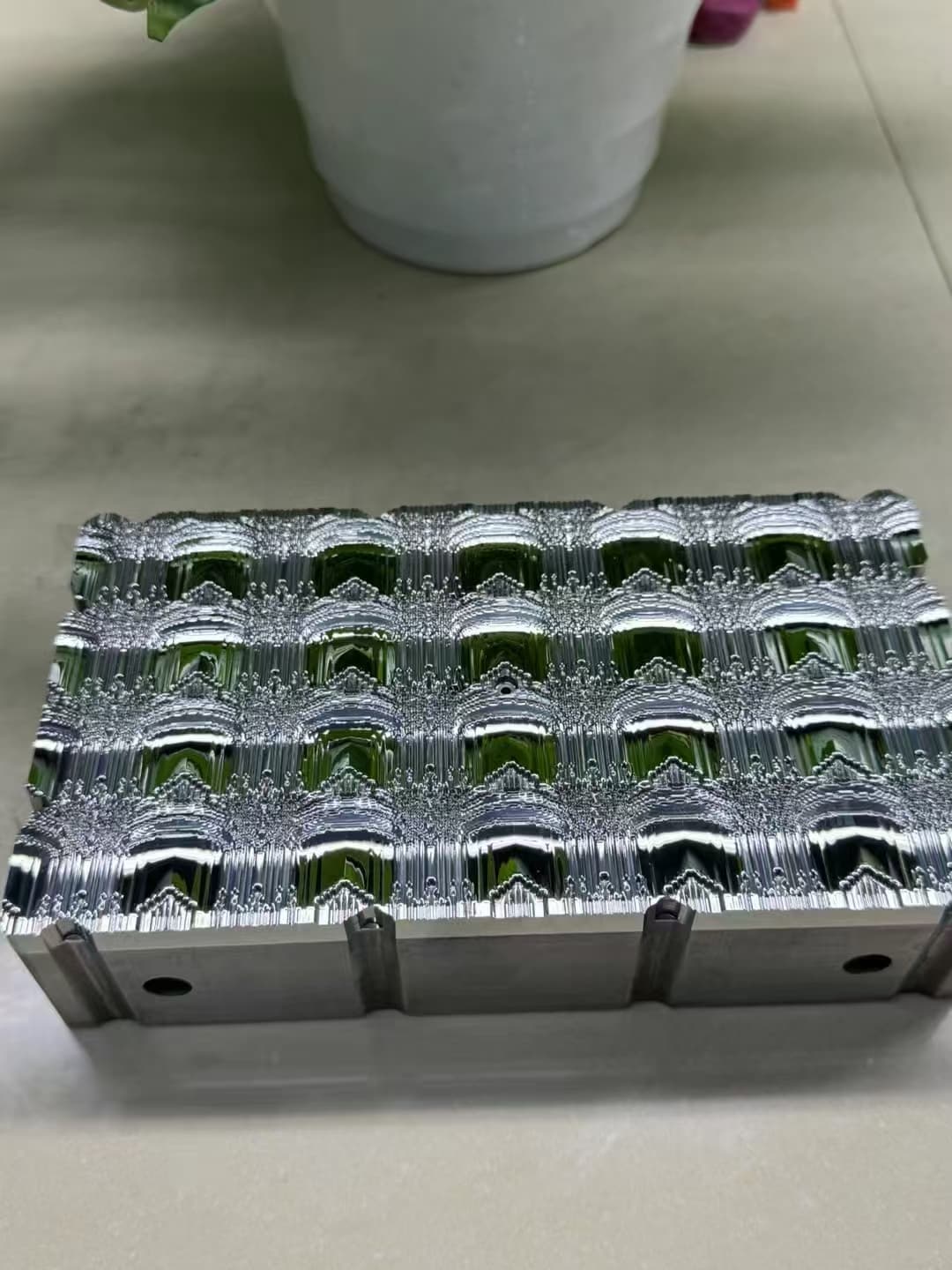
Factors Affecting Quality
- Material Properties: Different materials have varying hardness, toughness, ductility, and chemical stability, which affect the ease of polishing and the final result. For instance, glass materials require finer abrasives and stricter processes due to their hardness, while plastics are prone to scratches and deformation, requiring gentler methods.
- Polishing Tools and Materials: Proper selection of tools and materials is crucial. The material, hardness, and elasticity of polishing wheels, as well as the composition, concentration, and particle size of the polishing liquid, significantly impact the outcome. For example, wool polishing pads are suitable for soft materials, while harder materials may require more rigid tools like grinding pads.
- Process Parameters: Parameters such as polishing speed, pressure, time, and temperature play a vital role. Optimal speed and pressure ensure effective removal of surface defects while avoiding overheating, deformation, or new scratches.
- Environmental Factors: Cleanliness, temperature, and humidity of the environment must be controlled. Contaminants like dust or impurities can adhere to the workpiece surface, affecting the polishing results. Changes in temperature and humidity may alter the performance of polishing materials or cause thermal expansion and contraction of the workpiece, reducing accuracy.
-
Applications
- Optical Instruments: Precision components such as lenses and mirrors in microscopes, telescopes, cameras, and laser equipment require high-quality mirror optical polishing to ensure accurate light transmission and imaging performance.
- Electronic Devices: In fields like display screens, touch screens, and semiconductor chip manufacturing, mirror polishing enhances the transparency, flatness, and surface quality of materials such as glass substrates and silicon wafers, ensuring optimal device performance.
- Automotive Industry: Components such as car lights, rearview mirrors, and glass surfaces often employ mirror optical polishing to improve visual quality and optical performance, such as enhancing the brightness and range of car lights and reducing glare from rearview mirrors.