Casting Processes
Jan 13, 2025
I. Detailed Explanation of Casting Processes
(1) Sand Casting
-
Process Steps
- First, prepare patterns and core boxes. Patterns are used to shape the external contour of the castings, while core boxes form the internal cavities. These are typically made of wood, metal, or plastic.
- Next, prepare the molding sand, usually a mixture of raw sand, a binder (such as clay), additives (e.g., coal powder), and water. The sand is compacted around the pattern to form a sand mold. For castings with internal cavities, cores are made and placed in appropriate positions within the mold.
- Then, pour molten metal (e.g., cast iron, cast steel, or non-ferrous alloys) into the cavity of the sand mold through a gating system. The molten metal solidifies within the cavity to form the casting.
- Finally, after the casting has cooled and solidified, break the sand mold to retrieve the casting. The casting is cleaned and finished, removing excess material such as sand, risers, and gates.
-
Applications
- Sand casting is the most common casting method, suitable for castings of all sizes and shapes, especially large and complex ones. Examples include large cast iron machine tool bases, structural components for construction machinery, and complex automotive engine blocks.
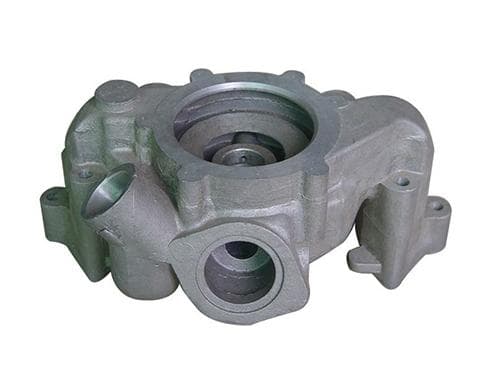
(2) Investment Casting
-
Process Steps
- First, create wax patterns using precision injection molding or other methods to shape the desired parts. These wax patterns require high accuracy, as they directly affect the final precision of the castings.
- Next, coat the wax patterns with multiple layers of refractory material, such as ceramic slurry. Each layer is dried to form a strong shell.
- Remove the wax by melting it, typically by placing the shell with the wax pattern into hot water or steam, leaving a hollow shell.
- Finally, fire the shell to increase its strength and permeability, then pour molten metal into it. After cooling and solidification, break the shell to retrieve the casting, followed by further finishing processes.
-
Applications
- Investment casting is primarily used for small, high-precision components with complex shapes, such as blades for aerospace engines and precision parts for medical instruments. It is widely used in industries where high accuracy and surface quality are critical.
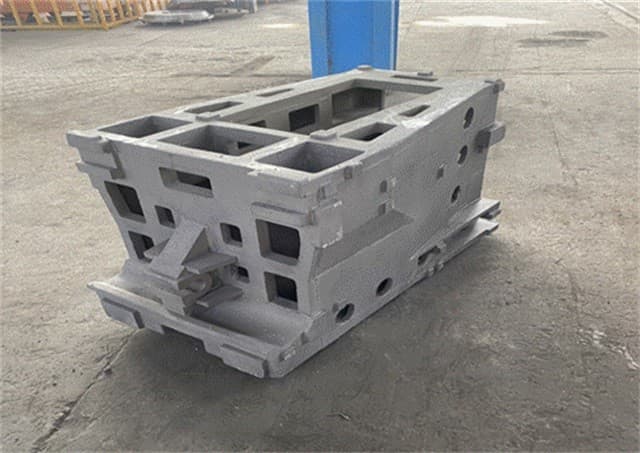
(3) Die Casting
-
Process Steps
- Die casting involves injecting molten or semi-molten metal into a mold cavity under high pressure, where it solidifies under pressure. The process begins with preparing the die-casting mold, which consists of movable and fixed dies, along with cooling and gating systems.
- Molten metal (such as aluminum or zinc alloys) is melted in a furnace and injected at high speed and pressure into the mold cavity using a die-casting machine. The metal solidifies quickly in the mold, and the casting is removed after the mold is opened.
- Because die casting operates under high pressure, the mold material, precision, and strength requirements are stringent to ensure product quality and mold durability.
-
Applications
- Die casting is ideal for thin-walled, complex-shaped, high-precision parts, such as aluminum alloy wheels, small aluminum alloy components of engines, and electronic device enclosures. It is highly efficient and suitable for mass production.
II. Advantages and Disadvantages of Casting Processes
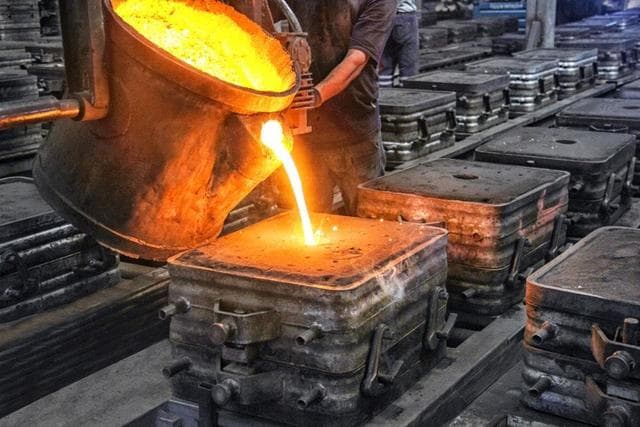
(1) Advantages
-
Strong Capability for Complex Shapes
- Casting processes can produce parts with intricate designs that other methods struggle to achieve. For instance, investment casting can form turbine engine blades with complex internal cooling passages.
-
Wide Material Compatibility
- Nearly all metal materials can be cast. Different metals can be chosen based on product performance requirements. For example, cast steel for high-strength parts, cast iron for wear-resistant components, and aluminum alloys for lightweight applications.
-
Cost Efficiency
- In batch production, the unit cost decreases as the production volume increases once the mold is completed. Sand casting is particularly cost-effective for large castings with moderate precision requirements.
-
Capability to Produce Large Parts
- Casting is suitable for manufacturing large parts, such as ship propellers and heavy equipment bases, which are challenging to produce with other methods.
(2) Disadvantages
-
Limitations in Dimensional Accuracy and Surface Quality
- Castings often have lower dimensional accuracy and rougher surfaces. Defects such as pores, sand inclusions, or slag can occur, requiring additional machining for improvement.
-
Internal Defects
- Internal issues like shrinkage cavities and porosity may reduce mechanical properties and potentially lead to failures under heavy loads.
-
Variable Production Efficiency
- Some processes, like investment casting, involve multiple steps, such as wax pattern making, refractory coating, and shell firing, leading to longer production cycles unsuitable for simpler parts.
III. Role of Casting in Modern Manufacturing
-
Foundational Importance
- Casting is a fundamental process in modern manufacturing. It is essential for shaping critical components in industries such as automotive, aerospace, and machinery manufacturing. For instance, engine blocks, machine tool bases, and columns rely on casting for their initial form.
-
Key for Large Structural Components
- Casting is indispensable for large structural parts like wind turbine hubs and bridge supports. These components require large sizes and complex shapes that only casting can provide.
-
Growing Importance in Precision Manufacturing
- Advanced casting techniques, such as investment casting and die casting, are increasingly applied in precision manufacturing. In aerospace, investment-cast high-temperature alloy blades meet extreme conditions, while die-cast aluminum enclosures in electronics ensure high accuracy and lightweight designs.
-
Integration with Other Processes
- Casting is often used alongside other processes, such as machining and heat treatment, to improve dimensional accuracy and enhance mechanical properties. For example, cast machine tool bases are machined for precision and treated to relieve stress, ensuring better stability and durability.